

Nationwide Maintenance
Here at West Fuel Systems Limited we understand the importance of regular fuel system maintenance as to ensure optimum performance and eliminate system down time. All responsible organisation should operate a planned maintenance program for fuel pipe line and tank testing with regular fuel tank inspections included within any maintenance schedule as to eliminate issues before they impact their business and the environment. With each of our comprehensive oil tank inspections been complimented with a full in depth site report to give our customers a complete overview of there current installation with any recommendations or compliance issues listed. We also undertake reactive maintenance with experienced engineers based in various location around the U.K. serving retail, commercial, marine, rail and domestic fuel systems.

Fuel Storage Tank Maintenance
-
Recommended annual maintenance visit.
-
Check the fuel tank for water and sludge build up.
-
Check fuel tank bunds for product and the sign of an overfill.
-
Check the operation of tank, pipework and environmental alarm sets.
-
Check the operation of valves.
-
Pressure test underground product lines.
-
Check operation and accuracy of tank gauging systems.

Precision Fuel Storage Tank and Pipework Testing
-
Calibrated ATEX approved high precision digital Mbar testing equipment.
-
Above and below ground fuel storage tanks
-
Above and below ground pipework systems.
-
Full test report and certification.

Environment Agency and DEFRA Oil Tank Inspections
-
Environment agency recommended annual inspection.
-
Check compliance with current Environment Agency guidelines.
-
Advise of any deterioration of the installation.
-
Recommend any appropriate new products that may provide additional protection against fuel loss.
-
Full detailed site report listing any compliance issues.
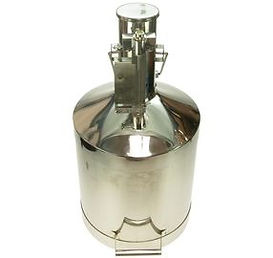.jpg)
Planned Fuel Pump Maintenance Inspections
-
Recommended annual maintenance visit.
-
Check calibration of dispensing meter with a calibrated measure can and adjust accordingly.
-
Check for leaks on gaskets and joints of all components.
-
Check the condition and operation of fuel hoses and nozzles.
-
Check and clean/replace fuel filters.
-
Check operation of register, pumping unit and electric motor and report any significant deterioration.
-
Check the condition of panels, locks and glass windows and seals. Advise if repair or replacement is necessary.

DSEAR Risk Assessments
-
Conduct a detailed technical risk assessment of all operations and procedures involving potentially dangerous substances.
-
Advise on actions to reduce or eliminate the risk.
-
Carry out a hazardous area survey and classification.
-
Examine hazardous areas to ensure that correctly rated electrical and mechanical equipment is being used (ATEX rated).
-
Implement arrangements to deal with accidents and emergencies.
-
Provide information, instruction and training on DSEAR to all employees.
-
Identify dangerous substance storage and processing areas.
-
Introduce measures to protect against explosions.
.jpg)
Reactive Maintenance
-
Above and below ground storage tanks
-
Dispensing pumps
-
Submersible pumps
-
Pump sets
-
Pipework
-
Gauges
-
Filtration equipment
-
Environmental alarms
-
Groundwork's